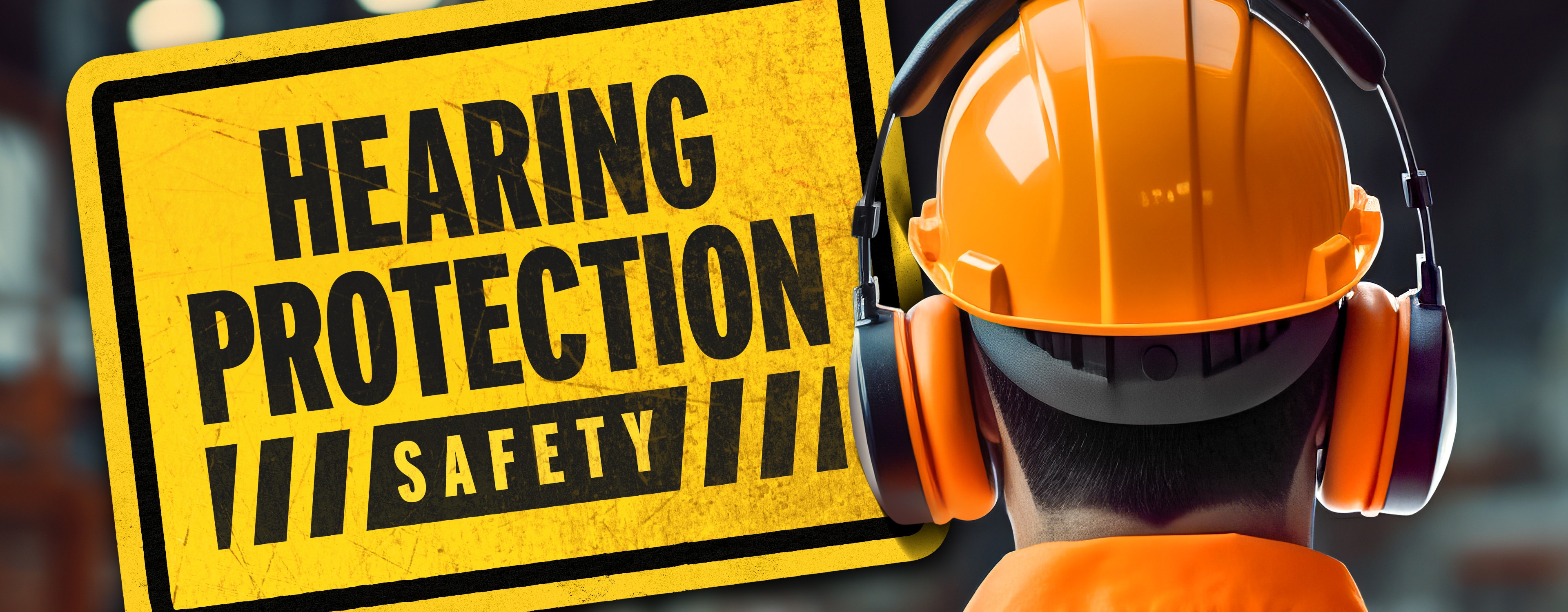
Whether setting up a warehouse or trying to improve workplace safety in your brewery, protecting hearing in commercial settings is vital to ensuring the safety and well-being of employees. Exposure to high levels of noise can lead to hearing loss and other health issues, making the use of hearing protection equipment essential in various industries. In environments where noise levels exceed the recommended thresholds, employers must implement hearing conservation programs to protect workers. By putting these programs in place and prioritizing hearing protection safety, businesses can create a safer and healthier work environment for their employees and comply with industry regulations.
Shop All Ear Plugs and Safety Ear MuffsOSHA Noise Standard
The Occupational Safety and Health Administration (OSHA) has established regulations to protect workers from the harmful effects of noise exposure in the workplace. The OSHA noise standard, found in 29 CFR 1910.95, limits occupational noise exposure to safeguard employees from hearing loss and other health issues.
The OSHA noise standard specifies a permissible exposure limit of 90 A-weighted decibels (dBA) as an 8-hour time-weighted average. This means employees should not be exposed to noise levels exceeding 90 dBA over an 8-hour work shift. OSHA also sets an action level of 85 dBA, which serves as a trigger for employers to implement a hearing conservation program. When noise levels reach or exceed 85 dBA, employers must provide hearing protection, conduct noise monitoring, offer training, and perform regular hearing tests for employees.
What Is a Noise Assessment?

The primary purpose of a noise assessment is to identify and evaluate the potential sources of hazardous excess noise that may pose a risk to employees' hearing. By conducting a noise assessment, businesses can determine whether the noise levels in their facility exceed recommended exposure limits set by regulatory agencies such as OSHA.
During a noise assessment, specialized noise measurement equipment, such as sound level meters or noise dosimeters, is used to quantitatively measure the noise intensity in decibels (dB). These measurements help assess the overall noise exposure levels and identify areas or processes where noise levels are highest.
How to Conduct a Noise Assessment
- Select the Right Tools - Utilize professional-grade noise level meters or dosimeters to accurately measure the noise levels in different areas of your facility. These tools provide objective data essential for determining potential risks and taking appropriate actions.
- Identify Noise Sources - During the assessment, identify the primary noise sources within your facility. Machinery, equipment, and processes that generate high noise levels should be identified to understand where noise control measures are needed.
- Measure Noise Levels - Measure noise levels at various locations and during different times of the day to capture a comprehensive understanding of the noise exposure in your workplace. This data will help evaluate the overall noise environment and determine if employees are at risk of hearing damage.
- Assess Employee Exposure - Evaluate the duration and intensity of noise exposure for employees working in different areas of your facility. Determine the daily exposure levels and compare them to regulatory standards to gauge the potential risk to employee hearing health.
- Document Findings - Record all data collected during the noise assessment process. This documentation will serve as a reference point for future assessments, help in tracking changes in noise levels over time, and provide a basis for implementing effective control measures.
- Implement Control Measures - Based on the findings of the noise assessment, implement appropriate control measures to reduce noise levels and protect employee hearing. This may include engineering controls, administrative controls, and personal protective equipment like earplugs or earmuffs.
- Monitor and Review - Regularly monitor noise levels in your facility to ensure that control measures are effective in maintaining a safe working environment. Review the noise assessment findings periodically to identify any new noise sources or changes in noise exposure levels.
Commercial Noise Hazards

Exposure to excessive noise levels in commercial settings poses a significant risk to workers' hearing health. Identifying common noise sources in the workplace is one of the most important steps in creating a safe and healthy environment for employees.
- Machinery and Equipment - Industrial machinery, such as compressors, generators, and manufacturing equipment, can generate high noise levels during operation. Heavy-duty tools like drills, saws, and grinders are more examples of common noise sources in construction and maintenance settings.
- HVAC Systems - Heating, ventilation, and air conditioning (HVAC) systems in commercial buildings can produce noise from fans, motors, and air circulation components. Improper installation or maintenance of HVAC units may also increase noise levels in workspaces.
- Construction Activities - Construction sites are notorious for high noise levels generated by activities like drilling, hammering, and heavy equipment operations. Workers in the construction industry are particularly vulnerable to noise-induced hearing loss without adequate protection.
- Vehicles - Vehicles, aircraft, and trains are significant noise sources in transportation-related industries. Workers involved in loading and unloading operations, maintenance, or driving may be exposed to high noise levels, requiring appropriate hearing protection.
- Entertainment Venues - In venues such as concert halls, nightclubs, and bars, loud sounds like music, cheering crowds, and amplified sound systems contribute to high noise levels. Workers in these settings such as staff and technicians, should use hearing protection to safeguard their hearing.
Noise Control Measures
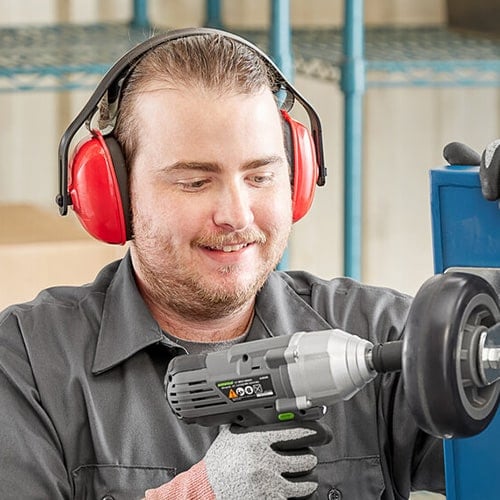
Implementing effective noise control measures is crucial in any commercial setting to protect the hearing health of employees and maintain a safe work environment. Here are some key strategies to help reduce noise levels in the workplace:
- Engineering Controls - Utilizing engineering controls involves modifying equipment or processes to reduce noise at the source. This can include installing noise-reducing barriers, enclosures, or mufflers on machinery, as well as using quieter equipment whenever possible.
- Administrative Controls - Implementing administrative controls involves adjusting work practices or schedules to minimize exposure to loud noises. This can include rotating employees to different tasks to limit their time in noisy areas, providing quiet zones for breaks, and establishing noise level monitoring programs.
- Personal Protective Equipment (PPE) - In situations where noise levels cannot be sufficiently reduced through engineering or administrative controls, personal protective equipment, such as earplugs or earmuffs, is essential. Employers should provide appropriate hearing protection devices and ensure employees are trained on their proper use and maintenance.
- Maintenance and Inspection - Regular maintenance and inspection of machinery and equipment can help identify and address sources of excessive noise. Proper lubrication, alignment, and equipment repair can help prevent noise levels from escalating and ensure a quieter workplace environment.
- Sound Absorption - Installing sound-absorbing materials, such as acoustic panels or ceiling tiles, can help reduce reverberation and echo in noisy environments. This can help improve speech intelligibility and create a more comfortable working environment for employees.
Hearing Protection Equipment

When it comes to ensuring the safety and well-being of employees in noisy work environments, providing appropriate hearing protection equipment is crucial. There are several types of hearing protection equipment available, each designed to address specific needs and preferences.
- Earplugs - Earplugs are small, disposable devices inserted into the ear canal to reduce the amount of sound entering the ear. They are lightweight, portable, and offer a high level of noise reduction. Foam earplugs are a popular choice as they conform to the shape of the ear canal, providing a secure fit and effective noise attenuation.
- Earmuffs - Earmuffs consist of ear cups connected by a headband worn over the head. They create a seal around the ears to block out noise and are often adjustable to ensure a comfortable fit. They are reusable and durable, making them a cost-effective option for long-term use in loud environments.
- Canal Caps - Canal caps combine the features of earplugs and earmuffs by providing a hybrid design that offers ear canal protection and over-the-head earmuff support. This design allows for a secure fit while providing enhanced noise reduction capabilities.
- Safety Signage - Clear and prominent safety signage indicating areas where hearing protection is required must be placed to remind employees to wear their protective gear, helping prevent unnecessary exposure to loud noise.
When Is Hearing Protection Required?
According to OSHA, employees must wear hearing protection if exposed to an average noise level of 85 decibels or higher over an 8-hour workday. Additionally, when noise levels reach 90 decibels or above, the allowable exposure time decreases, requiring more immediate action to protect workers' hearing. Exposure to high noise levels can lead to irreversible damage to the auditory system, making it essential to implement hearing protection measures when necessary.
Hearing Protection Training

Proper training on hearing protection is required to ensure employees are up-to-date on current hearing safety protocols. Employees exposed to high noise levels should receive regular training on the importance of using and maintaining hearing protection devices correctly.
- OSHA Regulations - OSHA mandates that employers train workers exposed to noise levels at or above 85 decibels over an 8-hour workday. Employers must offer hearing protection devices and ensure that employees are properly trained in their use.
- Maintenance and Care - Employees should be trained on the proper maintenance and care of hearing protection devices. Regular cleaning and inspection of the devices are required to check they provide the intended level of protection.
- Fit Testing - Fit testing is essential to confirm that hearing protection devices are correctly fitted to each employee. Training should include information on how to conduct fit testing and how often it should be performed.
- Monitoring and Compliance - Employers should monitor employee compliance with wearing hearing protection devices and provide ongoing training and support to reinforce the importance of protecting their hearing in the workplace.
Providing your staff with the right equipment, such as earplugs or earmuffs, significantly reduces the risk of noise-induced hearing loss and other auditory issues. Additionally, ensuring that your employees are trained on the importance of wearing hearing protection and how to use and maintain hearing protection equipment properly will go a long way in protecting their hearing. Prioritizing hearing protection safety in your workplace not only creates a healthier environment, but also could increase comfort and productivity among your workforce.